Lean Production
Zeit und Geld spielen in jedem Unternehmen eine wichtige Rolle. Neben dem sinnvollen und sparsamen Einsatz von Betriebsstoffen aber auch Personalressourcen ist die Produktionsleistung zu steigern. Gleichzeitig ist es möglich, die dafür anfallenden Kosten zu senken. Dafür aber wird die Lean Production benötigt.
Was bedeutet Lean Production?
Der Begriff Lean Production kommt aus dem Englischen und bedeutet übersetzt so viel wie „schlanke Produktion“. Mit dem Begriff Lean Production, auch Lean Manifacturing genannt, wird der Einsatz von Produktionsfaktoren, etwa Personal, Werkstoffe, Organisation und Betriebsmittel bezeichnet, bei dem auf Sparsamkeit und Zeiteffizienz geachtet wird. Ein wesentliches Augenmerk wird dabei auf eine Prozessoptimierung gelegt, um neben der Qualität auch die Flexibilität eines Unternehmens zu steigern bzw. zu optimieren. Um Lean Production erfolgreich anwenden zu können, bedarf es einer sauberen und klar definierten Lean Organisation.
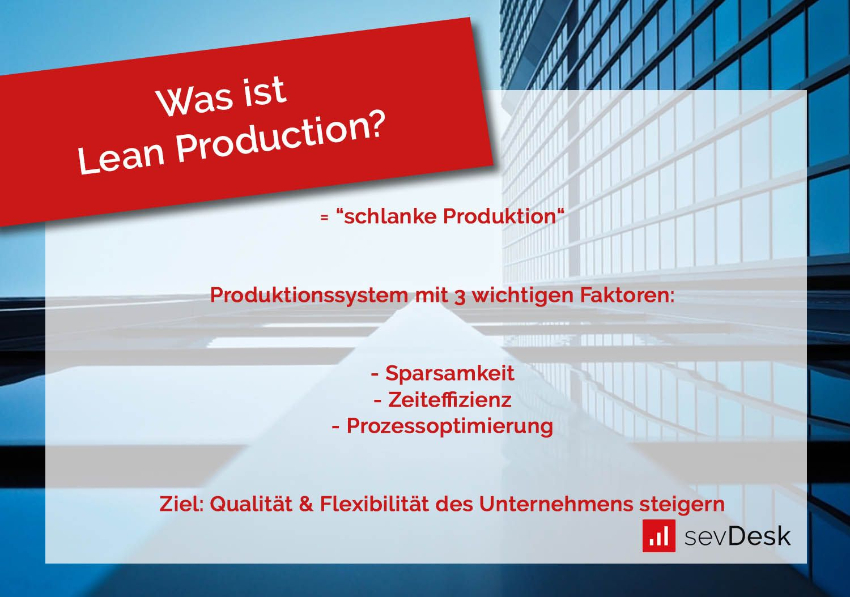
Was sind typische Merkmale der Lean Production?
Die Methode der schlanken Produktion weißt einige ganz typische Merkmale aus. Diese lauten:
- Just-in-Time- Produktion, auch One Piece Flow genannt
- Qualitätsmanagement zur Vermeidung von Fehlern
- Lean Operation mit einer geringen Lagerhaltung
- Teamarbeit
- Personalpolitik, bei der das Mitarbeiterengagement im Vordergrund steht
Woher stammt das Konzept der Lean Production?
Der Ursprung des Lean Managements ist Anfang der 1950er Jahre zu finden. Zu dieser Zeit befassten sich die ersten Techniker in der Automobilindustrie damit, neue Produktionssysteme zu finden. Der Fokus wurde dabei auf Methoden gelegt, die schlanker und effizienter sein sollten. Schon damals erkannte man, dass es für ein erfolgreiches Bestehen am Markt wichtig ist, bestimmte Prozesse so aufeinander abzustimmen, damit sie konstruktiver und ökonomischer werden. Vor allem das Unternehmen Toyota gilt als der Vorreiter der Lean Production schlechthin. Das Produktionssystem dieses Unternehmen wurde zum Vorbild und auch Maßstab für viele andere Unternehmen. Besonderen Wert legte man bei Toyota, nicht nur Prozesse technischer Natur zu beschreiben. Vielmehr widmete man sich dort dem Ziel, einen Idealzustand der Produktion durch viele Techniken und Prinzipien zu schaffen.
Was macht eine Lean Production sinnvoll?
Die Lean Production ist für ein Unternehmen aus vielerlei Hinsicht sinnvoll. Mit Lean Production ist es möglich, kürzere Durchlaufzeiten zu schaffen. Überdies wird die Produktivität stark erhöht und die Produkte werden in einer einwandfreien Qualität hergestellt. Auf der anderen Seite wird erreicht, dass die Verschwendung auf ein Minimum zu senken ist und die Geschwindigkeit in der Produktion erhöht wird. All diese Faktoren bringen im Endergebnis eine deutliche Kosteneinsparung.
Zusammenhang zwischen Lean Production und Lean Management
Um sich erfolgreich auf dem Markt zu behaupten, sind die Lean Production und das Lean Management wesentliche Herausforderungen, denen sich ein Unternehmen stellen muss. Schlanke Produktion und schlanke Strukturen stellen in Bezug auf die Umsetzung von Prozessorientierung und gleichzeitiger Kundenorientierung ein sportliches Ziel dar. Nur wer sich dieser Herausforderung stellt, wird sein Überleben in einem Markt, der von unstabilen Bedingungen geprägt ist, sicherstellen.
Wichtige Grundbegriffe zum Thema Lean Production
Es gibt einige wichtige Grundbegriffe zur Lean Production, welche du auf jeden Fall kennen musst:
Das Lean Management wird vor allem, bedingt durch die Vorreiterrolle von Toyota, von japanischen Begriffen geprägt. Deshalb kommen noch weitere wichtige Begriff hinzu:
Lean Production Methoden – Die acht Grundsäulen schlanker Produktionssysteme
In ihrer Anfangszeit bestand seitens der Arbeitnehmer wenig Akzeptanz gegenüber der schlanken Produktion. Vielmehr gab es den Irrglauben, dass es sich hier um Maßnahmen zur Rationalisierung handelt. Schnell wurde damals aber jedem bewusst, dass Lean Production nur dann ein Erfolg werden kann, wenn sich das gesamte System nach nur einem zentralen Punkt ausrichtet. Und dieser zentrale Punkt hieß Kundennutzen. Dieses Denken verhalf der Lean Production schließlich auch zum Erfolg. In Deutschland wurde dieses Produktionssystems schnell unter der Bezeichnung „ganzheitliche Produktionssysteme“ bekannt, mithilfe der Methoden der schlanken Produktion. Unterschieden wird hierbei zwischen acht Grundsäulen.
- Die Vermeidung von Verschwendungen: Die Verschwendung (Muda) stellt das Gegenstück zum Wert dar. Deshalb gilt es, Verschwendungen zu vermeiden und den Wert zu steigern. Alle Produktionsfaktoren müssen minimiert werden, wenn sie nicht zu einem Wertzuwachs beitragen. Überdies muss die Organisation von Abläufen ressourceneffizient ausgerichtet sein und einerseits die Verschwendung zu senken und die Durchlaufzeiten zu verbessern. Die Lean Production ist eine Möglichkeit, für eine Produktion der Nachhaltigkeit zu sorgen.
- Kontinuierlicher Verbesserungsprozess (Kaizen): Das Streben nach Perfektion ist das Ziel von einem ganzheitlichen Produktionssystem. Um dies erreichen zu können, bedarf es einem ständigen Vorantreiben der Verbesserungen von bestehenden Systemen und Prozessen. Um dies erreichen zu können, ist es zwingend notwendig, die Mitarbeiter in diesen kontinuierlichen Verbesserungsprozess mit einzubeziehen. Das bedeutet aber auch, dass jeder einzelne Mitarbeiter alle Abläufe, alle Methoden und auch alle Werkzeuge hinterfragen muss. Nur so kann eine Verbesserung erzielt werden. Viele Unternehmen lösen dies mit einem betriebsinternen Verbesserungsvorschlagsmodell.
- Standardisierung: Mit der Standardisierung wird die ständige Flexibilität abgelöst. Das Ziel hierbei ist eine Varianz von geringer Größe zwischen der Produktion und Prozessergebnissen, welche nicht vorhersehbar sind.
- Null-Fehler-Prinzip: Mit dem Null-Fehler-Prinzip wird eine Weitergabe von Fehlern in die nächste Prozesseinheit verhindert. In den standardisierten Ablauf werden Qualitätskontrollen integriert.
- Fließprinzip: Nach dem Fließprinzip läuft die ideale Lean Production ab. Das bedeutet, dass sowohl Produktion, Marketing als auch Verkauf sich in einem Fluss befinden. Von Anfang bis zum Ende ist alles durch einen Teilprozess verbunden. Diese Teilprozesse bauen damit aufeinander auf.
- Pull-Prinzip: Mit dem Pull-Prinzip wird eine Produktion bezeichnet, die ihre Ausrichtung rein auf die Kundenbedürfnisse hat. Die Produktion reagiert hier auf die Nachfrage auf dem Markt. Auf eine Flutung des Marktes mit Produkten wird hier verzichtet.
- Lean Leadership: Hier handelt es sich um die Mitarbeiterorientierung und eine zielorientierte Führung. Im Fokus steht eine Informationsweitergabe in flachen Hierarchien. Die Bereichsleiter müssen hier Flexibilität zeigen und für eine gute Einbindung sorgen.
- Visuelles Management: Das visuelle Management sorgt für eine optische Verdeutlichung. Damit ist durchaus die Vorgehensweise mit Marketing-Strategien zu vergleichen. Visuelles Marketing bedeutet mit Übersichtsfotos, mit Hinweisen und Ablaufplänen am Arbeitsplatz zu Dies sorgt für die nötige Aufmerksamkeit und eine Einhaltung der Prozesse und Vorgänge.
TIMWOOD – Die 7 Verschwendungsarten
Die klassische Lean Production Lehre nach Talichi Ohno unterscheidet zwischen 7 Verschwendungsarten.
Transport
Der Transport wird zu den notwendigen Verschwendungen gezählt. Der Grund darin liegt, dass es bei jedem Fertigungsprozess notwendig ist, Materialien durch die Produktion zu transportieren. Ziel ist es allerdings, die Verschwendung in diesem Bereich so minimal wie möglich zu gestalten.
Inventory
Mit hohen Beständen werden die in einer Wertschöpfungskette bestehenden Probleme verborgen. Sie verdecken einige Schwachstellen, die an anderen Stellen entstehen können oder bereits bestehen. Mit hohen Beständen werden für jedes Unternehmen Kapitalbindungskosten verursacht. Dies erhöht das Risiko einer Wertminderung, beispielsweise durch Veralterung.
Motion
Die Produktivität wird durch unnötige Bewegung gesenkt. Zur unnötigen Bewegung gehört sowohl die Ausführung in kleinerem Umfang, als auch im großen Ausmaß. Kleinere Bewegungen werden beispielsweise durch eine schlechte Ergometrie am Arbeitsplatz verursacht. Größere Bewegungen können durch Mitarbeiter verursacht werden, die entweder ständig in ihrem Arbeitsbereich unterwegs sind oder gar den Bereich zur Beschaffung verlassen müssen.
Waiting
In dem Zeitraum des Wartens findet keine Aktivität statt. In dieser Phase kann der Mitarbeiter nichts zur Wertschöpfung am Produkt beitragen. Wartezeiten werden beispielsweise verursacht durch nicht eingetroffenen Nachschub an Material oder auch durch das Warten auf das Ende von einem Bearbeitungsvorgang an einer Maschine. Der Vorgängerschritt ist nicht beendet und der Nachfolgeschritt kann deshalb nicht gestartet werden.
Over-Production
Der Zustand der Over-Production ist immer dann gegeben, wenn die Produktion höher ist, als die Abnahme durch Kunden. Aus einer Überproduktion werden Lagerbestände generiert, die Kosten verursachen, weil es keine Abnehmer gibt. Es wird zwar auf den ersten Blick durch die Herstellung der Produkte eine Wertschöpfung betrieben. Es besteht aber immer das Risiko, dass daraus durch den Kauf von Kunden auch Umsatz generiert wird oder es beim Lagerbestand bleibt.
Over-Engineering
Fallen Prozesse oder Fertigungsverfahren umfangreicher aus als sie eigentlich müssten und ohne Notwendigkeit für das Produkt sind, wird von Over-Engineering gesprochen. Dies passiert vor allem dann, wenn im Laufe der Zeit keine Anpassung der Technologie oder der Prozesse für die Herstellung stattgefunden hat.
Defects
Defects betrifft Ausschuss oder die Nacharbeit von Produkten aufgrund schlechter Qualität. In diesem Fall fand bereits ein Teil der Wertschöpfung statt. Im schlimmsten Fall sogar vollständig. Dies fällt sehr oft in der Endkontrolle des Produktes statt. Bei einer möglichen Nacharbeit ist die Wertschöpfung teilweise, bei Ausschuss sogar vollständig verschwendet und muss wiederholt werden.
Wichtige Kennzahlen bei einer Lean Production
Erfolg ist nur möglich, wenn ein Messen und Steuern stattfindet. Oft kann schon eine Messung von bestimmten Kennzahlen einen ersten Erfolg mit sich bringen. Wichtig sind für die Lean Production vor allem folgende Kennzahlen.
Die Vor- und Nachteile der Lean Production auf einen Blick
Zunächst im kurzen Überblick die Vorteile der Lean Production:
Und abschließend die Nachteile einer solchen Produktion:
Welche Voraussetzungen müssen für die Lean Production erfüllt sein?
Das Ziel von Lean Production ist es, alles was mit Verschwendung in der Produktion zu tun hat, auszuschalten. Um die Produktion leistungsfähiger zu machen mithilfe von einem schlanken Produktionsprozess, sind aber einige Voraussetzungen notwendig.
- Kostentreiber identifizieren: Um Lean Production umzusetzen, ist die wichtigste Voraussetzungen zunächst alle Kostentreiber zu identifizieren. Es ist nur dann möglich an den richtigen Stellschrauben zu drehen um weiteres Potenzial zu schaffen, wenn die Schwachstellen bekannt sind.
- Produktionsprozesse standardisieren: Nur wenn alle Prozesse in der Produktion standardisiert sind und auf höchstem Niveau optimiert sind, ist die Grundlage für die Lean Production geschaffen. Dazu sind nicht viele Einzelschritte notwendig, sondern vielmehr eine Kombination von verschiedenen Managementkonzepten.
- Neuentwicklung von Prozessen: Überdies reicht es nicht aus, nur die Prozesse mit einem Standard zu versehen. Es gilt auch, dass neue und effizientere Produktionsprozesse geschaffen werden.
In welchen Bereichen ist die Lean Production besonders sinnvoll?
Der Begriff Lean Production stammt bekanntermaßen aus der Automobilindustrie und wurde vor allem von Toyota geprägt. Grundsätzlich macht die Lean Production vor allem in Bereichen der Massenfertigung besonders viel Sinn. Doch sie ist durchaus auch mit ihrem Ansatz als Chance für viele Branchen zu sehen. Schwachstellen zu analysieren, Verschwendung aufdecken und Geschäftsprozesse auf den Prüfstand zu stellen, machen fast in jeder Branche Sinn. Von einer schlanken Produktion können viele Unternehmen profitieren.
Lean Production am Beispiel Toyota
Grundlage für die heutige Lean Production war das Toyota-Produktionssystem, auch TPS genannt. Der damalige Vorsitzende der Toyota Motor Cooperation sah sich aufgrund von Sparmaßnahmen, einer Isolationspolitk und einer bestehenden Knappheit an Rohstoffen gezwungen, zu einer Just-in-Time-Produktion überzugehen. Er wollte damit erreichen, dass eine größtmögliche Produktion, eine bestmögliche Qualität und eine pünktliche Lieferung an den Kunden gewährleistet ist. Damit Toyota dieses Ziel erreichen kann, wurde auf folgende Bausteine gesetzt:
- Just-in-Time: Es sollte nur das produziert werden, was für die vorliegenden Kundenaufträge benötigt wurde. Durch eine Überproduktion sollten Lagerbestände vermieden werden. Auf der anderen Seite sollte aber auch nicht zu wenig produziert werden, denn sonst läuft man Gefahr, in eine Lieferunfähigkeit zu geraten.
- Kanban, Pull-Prinzip: Im Jahre 1947 entwickelte Taiichi Ohno von Toyota Kanban. Kanban stellt eine Methode zur Steuerung der Produktion dar. In dieser Steuerung wird ausgehend von einem Auftragseingang der komplette Herstellungsprozess ausgelöst. Produziert wird dabei nur das, was auch wirklich benötigt ist. Damit wurde das Ziel verfolgt, die Lieferfähigkeit zu optimieren und gleichzeitig die Materialbestände zu reduzieren.
- Kaizen: Kaizen setzt sich aus Kai (Veränderung) und Zen (zum Besseren) zusammen. Kaizen ist innerhalb vom TPS ein ganz wesentlicher Baustein. Unter Einbeziehung von allen Mitarbeitern gibt es einen ständigen Verbesserungsprozess. Dies bedeutet einen wichtigen Faktor zum Thema Kosteneinsparung. Kleine als auch große Vorschläge zur Verbesserung durch Mitarbeiter helfen nicht nur bei der Optimierung von Prozessen, sondern auch bei der Vermeidung von Verschwendung.
Six Sigma eine sinnvolle Ergänzung zur Lean Production?
Betrachtet man Six Sigma und Lean Production, dann wird man schnell feststellen, dass beide eigentlich überhaupt nichts miteinander zu tun haben. Es handelt sich um zwei ganz verschieden voneinander entwickelten Strategien. Es ist aber dennoch keine Seltenheit, dass beide Strategien miteinander kombiniert werden. Und es bleibt festzustellen, dass sie sich durchaus gut ergänzen. Bei Six Sigma wird auf Statistiken gesetzt und diese dienen als Basis für die Optimierung von Produktionsprozessen. Im Vordergrund stehen dabei in erster Linie die Kundenzufriedenheit und die Qualität des Produktes. Produziert ein Unternehmen nach der Strategie von Six Sigma, so bedeutet dies, dass nur 3 oder 4 Fehler von einer Million möglicher Fehler passieren. Six Sigma wird deshalb auch sehr oft als Synonym für Null-Fehler-Toleranz benutzt.
Zusammenfassung
Lean Production ist ein Produktionsansatz, der darauf abzielt, Prozesse schlanker, effizienter und ressourcenschonender zu gestalten. Ursprünglich von Toyota entwickelt, basiert das Konzept auf Prinzipien wie Just-in-Time-Produktion, kontinuierlicher Verbesserung (Kaizen) und der Reduzierung von Verschwendung (Muda). Ziel ist es, Durchlaufzeiten zu verkürzen, Produktivität zu steigern und Kosten zu senken, ohne dabei die Qualität zu beeinträchtigen. Wesentliche Methoden sind unter anderem das Pull-Prinzip, das Null-Fehler-Prinzip und standardisierte Arbeitsabläufe. Während Lean Production besonders in der Massenfertigung zum Einsatz kommt, profitieren auch andere Branchen von der Optimierung ihrer Prozesse. Trotz klarer Vorteile stellt die Umsetzung eine Herausforderung dar, da sie einen Wandel in Unternehmenskultur und Organisation erfordert.